Desalter applications
It is all too easy to forget that the primary function of the desalting system is the removal of inorganic chlorides and other water-soluble compounds from crude oil. One need not be a corrosion specialist to realize the acids that form from these compounds can do tremendous, long-term damage in downstream processes of the refinery (as the inspection of crude tower overhead condensers can prove). However, the desalting process has become the focus of attention in areas that are no longer limited to the simple removal of salts and water. Most critical of these recent areas of concern has been the degree to which the desalting system contributes to the load of volatile organic contaminants (VOCs) at the waste water system. In fact, the condition of the brine from a modern desalter is frequently under greater scrutiny than the condition of the desalted crude.
The Agar System 3 represents the first and only interface control system to utilize this understanding of the oil/water interface as the basis for control. The system consists of a minimum of two or a maximum of four Agar energy absorption instruments: three designated for service in the vessel and one installed upstream of the unit in the crude feed line. In the System 3 control scheme, these probes provide continuous 4 to 20 mA output signals that are proportional to the % water concentrations at their individual locations inside the desalter.
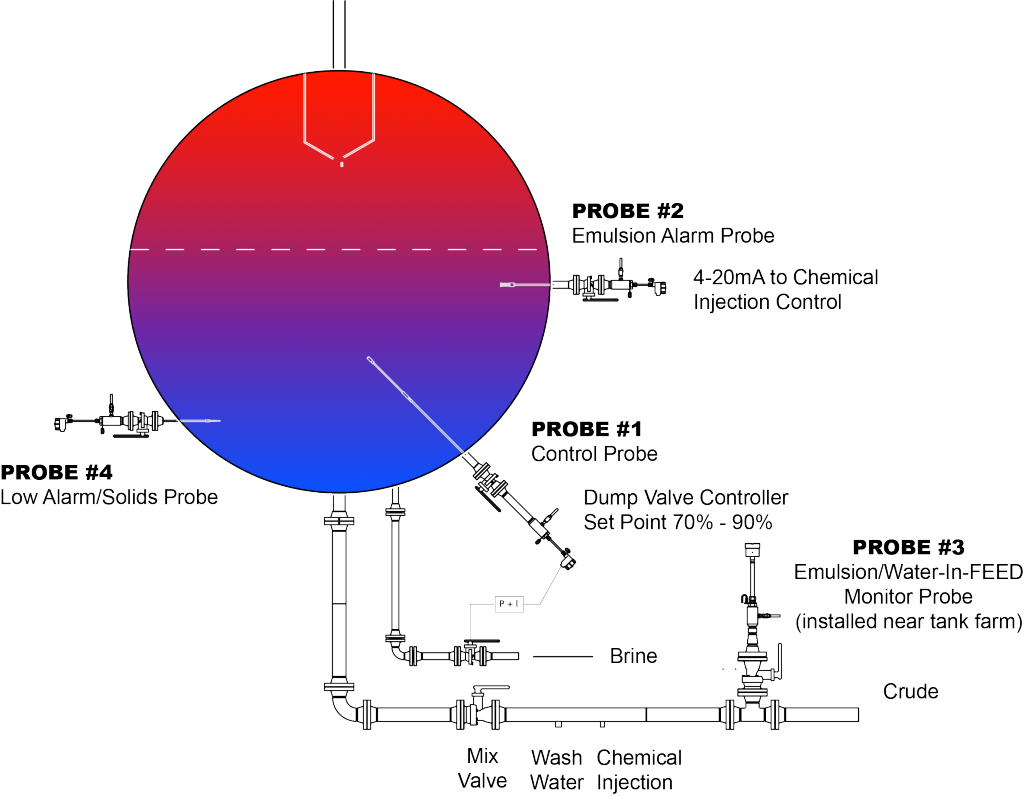
Probe #1
controls the brine outlet valve – using its ability to measure small amounts of oil in water to maintain a very high (and unstable) percentage of water several feet above the bottom of the vessel. This allows suspended oil in the water phase to separate, thus inhibiting oil undercarry as a primary control function. While Probe #1 establishes this lower limit for the emulsion layer anything that floats on the water phase stops here.Probe #2
monitors the % water content from its position in the oil phase just below the lower grid. This provides real-time detection of the rate and extent of emulsion growth (which must, by Probe #1’s control, occur in the upward direction). Probe #2’s monitoring function allows the operator to avoid downstream upsets by providing advanced warning of such growth, and allows time for the implementation of corrective measures to prevent grid loss (transformer „trip”).Probe #3
is an in-line monitor of the water content of the crude feed and is typically located as far as possible upstream of the desalter (generally at or near the tank farm). This probe provides advanced warning of wet/contaminated crude feed, which is necessary to avoid the upsets typically resulting from tank switching and/or the introduction of slop oil.Probe #4
monitors the condition of the water phase below the control probe, alarming on the presence of suspended oil that does not readily separate and threatens the condition of the brine effluent. This is of particular value when low-quality sources of wash water (e.g. stripped or straight sour water) are utilized that can upset the separation process and form stable oil-in-water mixtures (reverse emulsions). This probe is also used during mud-wash cycles.The benefits of this control scheme can be summarized as follows:
- Routine oil under carry is either significantly reduced or completely eliminated, providing both environmental and economical benefits.
- The operator is provided with a real-time „barometer” of conditions in both the oil and water phases of the vessel as well as the crude feed line.
- Upsets are detected long before their effects can be felt in downstream units, and the alarm outputs offer the option of automating upset response such as increasing or initiating chemical feed(s).
- Control action that constantly forces emulsion growth toward the electrical grids maximizes electrical work, allowing for optimization/reduction or, in some cases, elimination of chemical feed.
- By considering the location of an alarm signal, more information is provided as to the source of the upset (wash water quality, wet feed, etc.).
The Agar System 3 provides extensive information and control capabilities far beyond simple level control. Through measurement of percent water at specific points in the vessel and crude feed line, the overall behavior of the desalting process can be observed and the results optimized.
There can be no doubt that the operation of the desalting system is an exercise in compromise. A constant balance must be maintained between mixing intensity, wash water quality, chemical demulsifier feed, and control of other parameters that can provide optimal salt removal without forming an emulsion so tenacious that it compromises the system’s dehydration capabilities. Adding to this balancing act, new legislative demands placed on effluent water quality present the operator with a difficult challenge.
Optimizing the desalting process is a matter of optimizing the individual components and maximizing the efficiency of the electrostatic dehydration stage. By „pushing” the electrostatic process, one seeks to obtain the greatest amount of electrical work possible. The work performed near the grids can provide the dual benefits of enhanced salt removal (secondary mixing) and optimal coalescence.
Therefore, the question becomes how to maximize the electrical work of the grid.
In the vessel, the structural parameters such as vessel size, grid elevations and feed discharge points are all fixed. The most critical remaining variables become interface condition and location. In fact, optimal interface control has been proven to have significant impact on both the oil and water quality resulting from the dehydration process. Yet, in spite of the obvious need for such control, the traditional methods of control have operated on a fundamentally flawed assumption: Level. The very term „level control” indicates the presumption that the interface between oil and water in the desalter exists at a single point (such as that observed between gasoline and water). Any review of the internal conditions in the desalter vessel via the sample lines or swing-arm will dispel this notion. There is no level. Rather the interface consists of a transition zone from oil to water in a continuous change of volume percent. Understanding the true nature of the interface leads to the conclusion that efficient control comes from controlling these water/oil percentages and not an imaginary level.